Remont podłogi na gruncie w starym domu: Izolacja, materiały, etapy prac
Gdy zapadnie decyzja o unowocześnieniu czterech kątów, jednym z najbardziej niedocenianych, a zarazem kluczowych elementów, jest posadzka na najniższej kondygnacji. Przedsięwzięcie, jakim jest remont podłogi na gruncie w starym domu, to znacznie więcej niż tylko wymiana płytek czy paneli. To fundamentalna zmiana, która raz dobrze przeprowadzona, służy dekadami, a w skrócie oznacza kompletną przebudowę warstw podłogowych od gruntu w górę, zapewniając izolację termiczną i przeciwwilgociową. Bez tego komfort cieplny i trwałość reszty prac stoją pod znakiem zapytania, a późniejsza naprawa jest, mówiąc delikatnie, przedsięwzięciem rodem z filmów grozy – kosztownym i niszczącym.
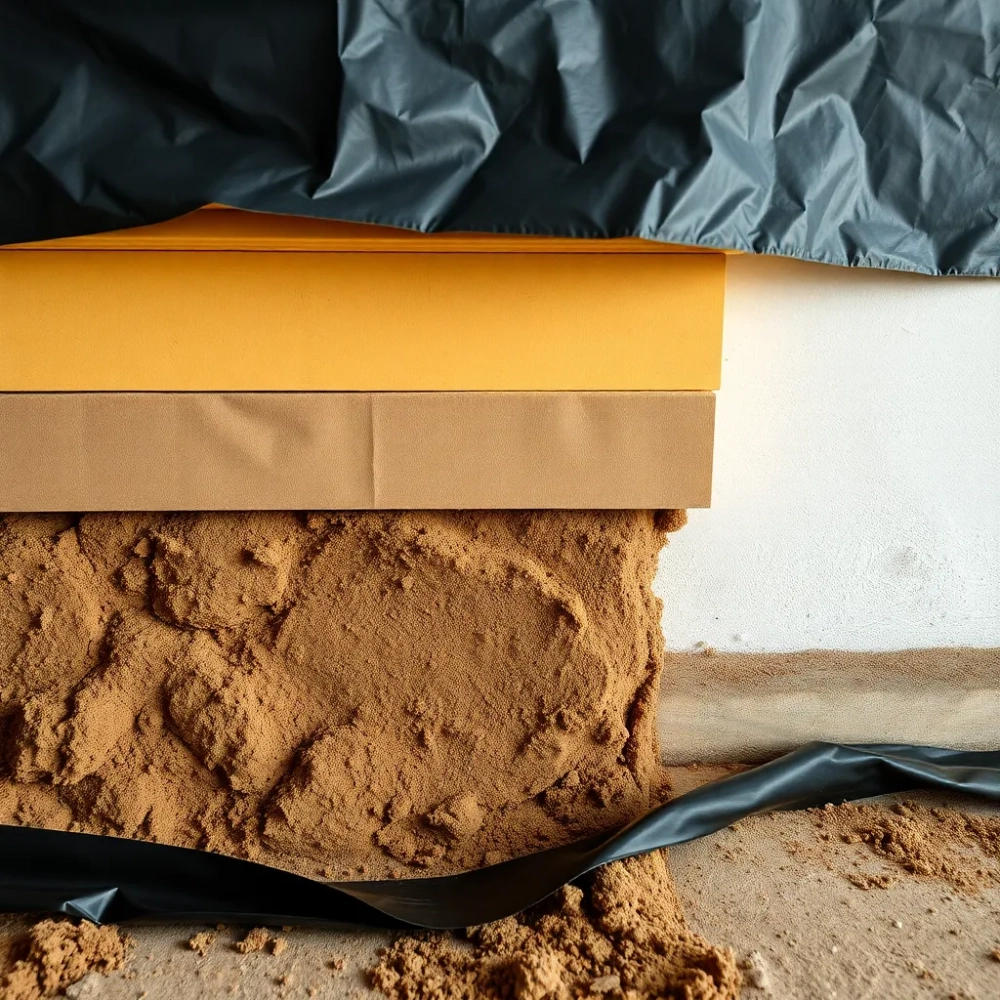
Przyglądając się projektom renowacji podłóg na gruncie, szybko dostrzegamy powtarzające się schematy warstw i orientacyjne koszty materiałów, które kształtują budżet inwestycji. Choć każda sytuacja jest inna, pewne etapy i wydatki są zaskakująco przewidywalne. Poniżej przedstawiamy przykładowe zestawienie warstw, ich funkcji oraz szacunkowych kosztów materiałowych za metr kwadratowy, opierając się na typowych rozwiązaniach spotykanych w projektach adaptacji starych budynków, aby dać pogląd na skalę przedsięwzięcia.
Warstwa | Funkcja | Typowa grubość [cm] | Szacunkowy koszt materiału [PLN/m²] |
---|---|---|---|
Podsypka (piasek/żwir) | Wyrównanie, zagęszczenie | 20-40 | 10-25 |
Chudy beton (chudziak) | Wyrównanie, podkład | 5-10 | 25-50 |
Hydroizolacja (papa/folia) | Ochrona przed wilgocią z gruntu | 1-2 warstwy | 10-30 |
Termoizolacja (EPS/wełna/XPS) | Izolacja cieplna | 10-30+ | 30-150+ |
Warstwa rozdzielająca/paroizolacja | Oddzielenie izolacji od wylewki / kontrola pary (jeśli wymagana) | folia | 3-8 |
Wylewka betonowa (jastrych) | Podkład pod posadzkę finalną | 5-8 | 30-60 |
Analizując te dane, łatwo zauważyć, że koszt materiałów to tylko część wydatków. Prawdziwym wyzwaniem, poza samą pracą fizyczną, jest precyzyjne wykonanie każdej warstwy, by synergicznie tworzyły skuteczną barierę przed chłodem i wilgocią, jednocześnie zapewniając stabilne podłoże dla przyszłych warstw wykończeniowych. Grubość izolacji termicznej znacząco wpływa na ostateczny koszt i przyszłe rachunki za ogrzewanie, co stanowi kluczowy element planowania.
A skoro mówimy o kosztach izolacji, przyjrzyjmy się bliżej cenom materiałów w zależności od potrzebnej grubości, aby osiągnąć założony współczynnik przenikania ciepła U. Współczesne normy wymagają wartości U na poziomie 0.15 W/m²K, ale celując w U poniżej 0.10 W/m²K, zyskujemy znacząco na komforcie i oszczędnościach. Porównajmy koszt materiału dla izolacji podłogi na gruncie, pozwalającej osiągnąć U=0.10 W/m²K, dla popularnych opcji. Pamiętajmy, że są to wartości orientacyjne i mogą się różnić w zależności od producenta i regionu.
Wybór materiałów izolacyjnych: Wełna skalna czy styropian?
Gdy stajemy przed wyzwaniem ocieplenia podłogi na gruncie w starym domu, pojawia się odwieczny dylemat: wełna skalna czy styropian? To trochę jak wybór między młotkiem a śrubokrętem – oba narzędzia świetne, ale do różnych zadań, a czasami potrzebujemy ich kombinacji. Decyzja nie jest trywialna i zależy od wielu czynników, w tym specyfiki projektu, budżetu i, co kluczowe, warunków panujących pod powierzchnią.
Na pierwszy rzut oka styropian, zwłaszcza polistyren ekstrudowany (XPS), wydaje się być oczywistym wyborem dla podłogi na gruncie. Jego zamkniętokomórkowa struktura charakteryzuje się bardzo niską nasiąkliwością, co jest absolutnie kluczowe w kontakcie z gruntem i potencjalną wilgocią. XPS ma też zazwyczaj wyższą wytrzymałość na ściskanie w porównaniu do popularnego styropianu fasadowego (EPS), co czyni go bardziej odpornym na obciążenia statyczne i dynamiczne z podłogi. Współczynnik przewodzenia ciepła lambda (λ) dla XPS jest często niższy (lepszy) niż dla EPS, oscylując w okolicach 0.032-0.034 W/mK.
Standardowy styropian podłogowy, oznaczany często jako EPS 100 lub EPS 200, ma odpowiednią wytrzymałość na ściskanie (odpowiednio ≥100 kPa i ≥200 kPa naprężenia ściskającego przy 10% odkształceniu), ale jego nasiąkliwość jest wyższa niż XPS. Oznacza to, że w miejscach, gdzie ryzyko podciągania kapilarnego czy zalewania jest duże, sam styropian EPS może nie być wystarczającą barierą. Lambda dla dobrego styropianu podłogowego mieści się zazwyczaj w przedziale 0.035-0.038 W/mK.
Z drugiej strony mamy wełnę skalną. Tutaj kluczowe jest wybranie produktu przeznaczonego specjalnie do izolacji podłóg, a mianowicie hydrofobowej wełny skalnej o podwyższonej gęstości, często w formie sztywnych płyt. Gęstość rzędu 100-150 kg/m³ i naprężenie ściskające na poziomie 40-60 kPa (lub więcej) zapewniają jej stabilność i odporność na obciążenia, choć zazwyczaj mniejszą niż w przypadku XPS czy nawet niektórych typów EPS. Współczynnik lambda dla wełny skalnej podłogowej to typowo 0.036-0.040 W/mK.
Największą przewagą wełny skalnej w niektórych aplikacjach podłogowych, szczególnie gdy podłoga ma być wykonana na legarach z pustką wentylacyjną pod spodem, jest jej paroprzepuszczalność i zdolność do częściowego odprowadzania wilgoci w formie pary wodnej. Działa też doskonale akustycznie, tłumiąc dźwięki uderzeniowe. Jej hydrofobizacja ogranicza wchłanianie wody, ale nie czyni jej całkowicie wodoodporną jak XPS.
W starych domach często spotykamy się z wyzwaniami w postaci nierównego podłoża czy istniejących struktur. Styropian, zwłaszcza w sztywnych płytach, wymaga stosunkowo równej i stabilnej powierzchni. Wełna, będąc nieco bardziej elastyczną, potrafi lepiej dopasować się do drobnych nierówności, ale w przypadku poważnych deformacji gruntu czy chudziaka, żadna izolacja nie uratuje sytuacji bez solidnego przygotowania podłoża.
Decyzja o wyborze materiału termoizolacyjnego wpływa nie tylko na cenę, ale także na sposób montażu i inne warstwy podłogi. Układając wełnę na chudziaku, musimy pamiętać o precyzyjnym ułożeniu szczelnej hydroizolacji POD wełną, a często i paroizolacji NA wełnie (przed wylewką). W przypadku styropianu (EPS/XPS), hydroizolacja również jest obowiązkowa POD izolacją, ale ryzyko przenikania pary przez sam materiał izolacyjny jest mniejsze.
A co z cenami? Tutaj, jak w życiu, diabeł tkwi w szczegółach, czyli w grubości. Aby uzyskać wymagane współczynniki U, musimy zastosować odpowiednią grubość materiału. Dla osiągnięcia U poniżej 0.15 W/m²K, minimalna grubość EPS lub wełny o dobrych parametrach lambda to często 15-20 cm, a dla ambiciozniejszych celów (np. U=0.10) może to być nawet 30-40 cm lub więcej. Cena metra sześciennego styropianu podłogowego jest zazwyczaj niższa niż metra sześciennego wełny skalnej o odpowiedniej gęstości do podłóg, nie mówiąc już o XPS, który jest najdroższy w przeliczeniu na m³. Patrząc na tabelę powyżej, różnice w kosztach materiału per m² przy tej samej skuteczności (U=0.10) są zauważalne.
W praktyce renowacyjnej zdarza się, że wybór podyktowany jest nie tylko parametrami, ale i łatwością transportu i montażu w ograniczonej przestrzeni starego domu. Wielkoformatowe płyty styropianu czy wełny wymagają pewnej logistyki. Cięcie i dopasowanie do kształtów pomieszczeń czy omijanie instalacji to rutyna, ale precyzja jest tu kluczowa, by uniknąć mostków termicznych w miejscach łączeń.
Wyobraźcie sobie sytuację: stary dom z wysokim poziomem wód gruntowych. Pomimo solidnego drenażu zewnętrznego, ryzyko wilgoci jest realne. W takim przypadku postawienie na hydroizolacja podłogi na gruncie w postaci podwójnej warstwy papy termozgrzewalnej pod izolacją, a na to grubą warstwę XPS o niskiej nasiąkliwości, wydaje się rozsądnym, a wręcz jedynym słusznym rozwiązaniem, mimo wyższego kosztu początkowego. Oszczędność w tym miejscu może zemścić się później permanentnym problemem z wilgocią.
Podsumowując ten segment (ale nie całego artykułu!): zarówno wełna skalna, jak i styropian (EPS, a zwłaszcza XPS) mają swoje miejsce w renowacji podłogi na gruncie. Wybór powinien być podyktowany szczegółową analizą warunków na placu budowy, planowanego układu warstw (na wylewce czy na legarach?), budżetu i pożądanych parametrów końcowych. Najważniejsze to użyć materiału o parametrach odpowiednich do zastosowania w kontakcie z gruntem (odporność na wilgoć, wytrzymałość na ściskanie) i zastosować odpowiednią, wystarczającą grubość, planując ją tak, aby mieściła się w dostępnej wysokości.
Kluczowa hydroizolacja podłogi na gruncie: Jak zapewnić szczelność?
Wilgoć. Odwieczny wróg budowlańca i każdej osoby remontującej stary dom. Grunt pod budynkiem to nie jest sucha pustynia, nawet jeśli na powierzchni jest idealnie. Wody gruntowe, opady wsiąkające w ziemię, wilgoć podciągana kapilarnie przez ściany fundamentowe – to wszystko czyha, by przeniknąć w głąb konstrukcji i zacząć siać spustoszenie. Dlatego też kluczowa hydroizolacja podłogi na gruncie to nie jest opcja, to absolutny mus, fundament sukcesu całego przedsięwzięcia. Można powiedzieć, że bez szczelnej bariery przeciwwodnej, całe ocieplenie i wylewka to "gwóźdź do trumny" dla naszej podłogi.
Najczęstszymi materiałami stosowanymi do hydroizolacji poziomej na gruncie są papy termozgrzewalne oraz grube folie z tworzyw sztucznych, przede wszystkim folie PE (polietylenowe) o grubości co najmniej 0.3 mm, choć lepsze są dedykowane folie przeciwwodne, które mają jeszcze lepsze parametry. W przypadku większych ryzyk wodnych, niektórzy inwestorzy stosują nawet maty bentonitowe, które pęcznieją w kontakcie z wodą, tworząc bardzo szczelną barierę, ale jest to rozwiązanie stosunkowo drogie i bardziej skomplikowane w aplikacji.
Wykonanie hydroizolacji musi być chirurgicznie precyzyjne. Zacznijmy od podstaw – podłoże musi być czyste, suche (na tyle, na ile to możliwe w kontakcie z gruntem przed izolacją) i pozbawione ostrych elementów, które mogłyby przebić papę czy folię. Chudy beton (chudziak), o którym wspominaliśmy, stanowi idealną, równą bazę. Niewielkie nierówności czy kruszywo mogą stać się "punktami ucisku" i spowodować uszkodzenie membrany pod ciężarem kolejnych warstw lub w wyniku osiadania.
Przy użyciu papy termozgrzewalnej, kluczem jest zapewnić szczelność poprzez odpowiednie zakłady i staranne zgrzewanie. Każdy pas papy powinien zachodzić na poprzedni z minimalnym zakładem 10 cm na krawędziach wzdłużnych i 15-20 cm na krawędziach poprzecznych. Zgrzewanie wykonuje się palnikiem, podgrzewając dolną powierzchnię papy i podłoże do momentu uplastycznienia masy asfaltowej, a następnie dociskając wałkiem. Krawędzie zakładów muszą być idealnie sklejone, bez żadnych szczelin czy pęcherzy powietrza. To wymaga wprawy i dbałości o detale.
Folie PE, choć prostsze w układaniu niż papa, również wymagają dbałości o detale. Pasy folii układa się na zakład minimum 20 cm, a najlepiej 30 cm. Każdy zakład, a także miejsca przebicia folii przez rury instalacyjne, muszą być starannie sklejone specjalną taśmą dwustronną lub klejem butylowym, dedykowanym do folii budowlanych. Przecięcia na rury powinny być minimalne, a miejsca przejść uszczelnione kołnierzami i taśmą. Im mniej łączeń, tym mniejsze ryzyko przecieków.
Widzieliśmy na własne oczy remont, gdzie ekipa poszła na skróty, kładąc zbyt cienką folię PE i oszczędzając na taśmie do zakładów. Kilka lat po remoncie na ścianach pojawiły się pleśń i wykwity solne, a podłoga "puchła" od wilgoci. Właściciel musiał zerwać całą podłogę aż do gruntu, co kosztowało go kilkakrotnie więcej niż pierwotne oszczędności na hydroizolacji. To studium przypadku boleśnie pokazuje, że hydroizolacja to nie miejsce na kompromisy.
Niezwykle ważnym, a często zaniedbywanym aspektem jest połączenie hydroizolacji podłogowej z hydroizolacją pionową na ścianach fundamentowych. Bariera przeciwwodna na podłodze musi szczelnie zachodzić na barierę na ścianie (lub podciągać się w górę ściany fundamentowej, tworząc "wanienkę" lub "koryto") na wysokość co najmniej 15-30 cm powyżej planowanego poziomu gotowej podłogi. Zakład ten powinien być również uszczelniony, np. zgrzewem papy do ściany (wymaga to wcześniejszego przygotowania ściany i gruntowania) lub szczelnym doklejeniem folii i jej dociśnięciem. Ten szczegół zapobiega przenikaniu wilgoci z gruntu w miejscu styku podłogi ze ścianą, gdzie powstaje "kąt".
Papa termozgrzewalna daje zazwyczaj większą pewność szczelności na dłuższą metę, pod warunkiem poprawnego wykonania. Folie są szybsze w montażu i tańsze, ale bardziej podatne na uszkodzenia mechaniczne w trakcie kolejnych etapów prac oraz na rozszczelnienie na zakładach, jeśli taśma straci swoje właściwości. Wybór materiału powinien być podyktowany poziomem wód gruntowych i ryzykiem zalewania. Jeśli woda stoi w wykopie po deszczu, sama folia 0.3 mm to za mało – potrzebna jest co najmniej podwójna warstwa papy lub dedykowana membrana przeciwwodna.
Zapewnienie idealnej szczelności wymaga skrupulatności. Każde przejście instalacji (rura kanalizacyjna, wodna) przez warstwę hydroizolacji jest potencjalnym mostkiem wilgotnościowym. Takie miejsca wymagają specjalnych kołnierzy uszczelniających, które są zgrzewane (do papy) lub sklejane (do folii), a następnie precyzyjnie obejmują rurę. Nawet najmniejsza nieszczelność może z czasem spowodować poważne problemy, o których przekonało się wielu pechowców, którzy zlekceważyli ten etap. To nie jest moment na "zrobimy na oko" czy "jakoś to będzie".
Pamiętajmy również o czasie. Papa termozgrzewalna wymaga odpowiedniej temperatury zewnętrznej do prawidłowego zgrzewania. Folie można układać praktycznie zawsze, ale są delikatniejsze. Niezależnie od materiału, warstwa hydroizolacji powinna być jak najszybciej przykryta kolejną warstwą (izolacją termiczną lub jastrychem), aby zminimalizować ryzyko jej uszkodzenia przez narzędzia, spadające elementy czy po prostu chodzenie po niej. Jeden niewidoczny gołym okiem otwór wielkości szpilki może w przyszłości doprowadzić do katastrofy.
Hydroizolacja to kręgosłup całej konstrukcji podłogi na gruncie. Jej poprawność wykonania definiuje długowieczność i funkcjonalność całego rozwiązania. Oszczędność na materiale lub wykonaniu hydroizolacji jest oszczędnością pozorną, która w najlepszym wypadku zaowocuje zimną podłogą, a w najgorszym permanentnym problemem z wilgocią, pleśnią i potencjalnym uszkodzeniem konstrukcji budynku. Dlatego tak kluczowe jest zastosowanie odpowiednich materiałów, zachowanie wymaganych zakładów, skrupulatne uszczelnienie każdego detalu i połączenie jej ze ścianami fundamentowymi.
Najczęstsze błędy przy remoncie podłogi na gruncie i jak ich uniknąć
Wydawać by się mogło, że położenie podłogi na gruncie to prosta sprawa – ot, parę warstw jedna na drugiej. Nic bardziej mylnego! To proces wymagający wiedzy, precyzji i, co najważniejsze, unikania pułapek. Na placu boju renowacji starych domów spotykamy powtarzające się scenariusze porażek, które można by ułożyć w swoisty "ranking wpadek". Znajomość tych Najczęstsze błędy przy remoncie podłogi na gruncie jest najlepszą strategią ich unikania, bo, jak mówi stare porzekadło, mądry Polak po szkodzie, ale jeszcze mądrzejszy przed.
Błąd pierwszy i fundamentalny, od którego często zaczynają się kłopoty, to niewłaściwe przygotowanie podłoża. Myślimy, że grunt pod budynkiem "już tam jest" i wystarczy wyrównać. Niestety, często jest on luźny, niejednorodny, pełen gruzu, korzeni czy innych niespodzianek po latach eksploatacji starego budynku. Brak odpowiedniego zagęszczenia warstwy nośnej z piasku czy żwiru powoduje, że po położeniu kolejnych warstw i obciążeniu podłogi, grunt zaczyna osiadać. Efekt? Pęknięcia w wylewce, odkształcenia, a nawet uszkodzenia warstw izolacji.
Jak tego uniknąć? Po usunięciu starej podłogi i dojściu do rodzimego gruntu, należy go starannie sprawdzić. Jeśli jest niejednorodny lub luźny, lepiej wybrać słabszą warstwę i zastąpić ją dobrze zagęszczonym, sporym nasypem żwirowym (np. kliniec 0-31.5 mm) lub grubym piaskiem. Warstwy nośne (tłuczeń, żwir, piasek gruby) powinno się układać po 15-20 cm i zagęszczać mechanicznie – skoczkiem lub walcem. Test laboratoryjny stopnia zagęszczenia (np. badanie VSS) przed wylaniem chudziaka to dla ambitnych, ale już sama wiedza o konieczności użycia odpowiedniego sprzętu do zagęszczania i wielokrotnego przejechania po każdej warstwie to podstawa. Chudy beton też powinien być zbrojony siatką i odpowiednio pielęgnowany (polewanie wodą), aby uniknąć pęknięć skurczowych, które mogą uszkodzić hydroizolację na nim położoną.
Błąd numer dwa, często idący w parze z brakiem poszanowania dla wilgoci: nieprawidłowe wykonanie lub brak kluczowej hydroizolacji podłogi na gruncie. Pisaliśmy o tym wcześniej, ale warto podkreślić: pominięcie tej warstwy, użycie zbyt cienkiej folii, brak zakładów, brak sklejenia zakładów taśmą lub nieprawidłowe zgrzanie papy, a przede wszystkim brak szczelnego połączenia izolacji podłogowej ze ścianami fundamentowymi (tzw. wanny hydroizolacyjnej) to prosta droga do katastrofy. Wilgoć podciągana kapilarnie w ścianach i przenikająca z gruntu znajdzie drogę do środka, powodując pleśń, grzyb, uszkodzenie materiałów izolacyjnych, a nawet konstrukcji drewnianych elementów (legary, ościeżnice drzwiowe na poziomie podłogi). Unikamy tego, stosując się do zasad opisanych w rozdziale o hydroizolacji – materiał z certyfikatem, podwójne zabezpieczenie w miejscach krytycznych, duuuże zakłady i perfekcyjne klejenie/zgrzewanie.
Błąd trzeci: zbyt mała grubość lub niewłaściwy rodzaj warstwy termoizolacyjnej. Czasem pokusa, by "zaoszczędzić" kilka centymetrów na wysokości (w starych domach każdy centymetr wysokości jest na wagę złota!) lub na cenie materiału, bierze górę. Efektem jest zimna podłoga, którą nawet najlepsze ogrzewanie nie zdoła odpowiednio nagrzać, a także wysokie rachunki za energię. Użycie styropianu fasadowego zamiast podłogowego o odpowiedniej wytrzymałości na ściskanie spowoduje jego uszkodzenie pod obciążeniem użytkowym, a to zniszczy również wylewkę. Wybranie wełny skalnej o zbyt niskiej gęstości do podłogi na legarach może prowadzić do jej opadnięcia i powstania pustek termicznych.
Jak uniknąć? Planuj grubość izolacji zgodnie ze współczesnymi normami (lub lepiej, celując w U poniżej 0.10), biorąc pod uwagę lambdę materiału. Sprawdź dokumentację techniczną materiału izolacyjnego pod kątem jego wytrzymałości na ściskanie (minimum 100 kPa dla EPS, odpowiednia gęstość dla wełny podłogowej) i nasiąkliwości (zwłaszcza dla styropianu, a idealnie używać XPS w miejscach podwyższonego ryzyka wilgoci). Pamiętaj, że to jest jedna z niewielu prac, której poprawa jest praktycznie niemożliwa bez totalnej demolki – raz położona izolacja jest "zakopana" na zawsze.
Błąd czwarty: niedociągnięcia w warstwie wyrównującej – wylewce. Wylewka (jastrych) ma za zadanie stworzyć idealnie gładką i równą powierzchnię pod wykończenie. Jej zły poziom, nierówności, brak dylatacji obwodowych (czyli szczeliny między wylewką a ścianami wypełnionej elastycznym materiałem) lub brak zbrojenia (jeśli jest potrzebne) mogą prowadzić do jej pękania, odrywania się od podłoża i problemów z montażem finalnej posadzki (paneli, płytek). W starych domach, gdzie ściany są nierówne, dylatacje są absolutnie kluczowe, aby uniknąć przenoszenia naprężeń z konstrukcji budynku na wylewkę.
Unikaj tego błędu, stosując wylewkę odpowiedniej grubości (zwykle 5-8 cm na izolacji), zawsze stosując dylatacje obwodowe wokół ścian i słupów, a także w dużych powierzchniach podłogi (>30-40 m²) czy w przejściach między pomieszczeniami. Wylewki na ogrzewaniu podłogowym bezwzględnie wymagają dylatacji i zazwyczaj zbrojenia siatką lub włóknami rozproszonymi. Pamiętaj o odpowiedniej pielęgnacji świeżo wylanej posadzki – chronieniu przed zbyt szybkim wysychaniem i przeciągami przez pierwsze dni.
Inne, choć również ważne błędy, to lekceważenie wentylacji (jeśli mamy pustkę pod legarami - musi być zapewniona wentylacja!), nieprawidłowe rozmieszczenie instalacji przebijających przez podłogę (rury, kable – każde przejście to potencjalny mostek termiczny i wilgotnościowy, który trzeba starannie zaizolować i uszczelnić), a także... pośpiech. Remont podłogi na gruncie wymaga czasu – na wyschnięcie chudziaka, na prawidłowe ułożenie i zabezpieczenie hydroizolacji, na dokładne docięcie i spasowanie izolacji, w końcu na związanie i wyschnięcie wylewki (co przy standardowych wylewkach cementowych trwa tygodniami – ok. 1 cm grubości na tydzień). Niecierpliwość może doprowadzić do zawilgocenia kolejnych warstw lub osłabienia ich parametrów.
Podsumowując (w obrębie rozdziału!): sukces renowacji podłogi na gruncie tkwi w szczegółach. Solidne przygotowanie podłoża, perfekcyjna hydroizolacja, odpowiednia grubość i właściwy rodzaj izolacji termicznej oraz starannie wykonana wylewka to filary trwałości i komfortu. Każdy z tych etapów, choć wydaje się oczywisty, kryje pułapki, których świadomość jest najlepszym ubezpieczeniem przed kosztownymi błędami. Nie oszczędzajcie na tych elementach, bo ocieplenie podłogi na gruncie w starym domu to inwestycja, która ma służyć latami.
Połączenie izolacji podłogi ze ścianami fundamentowymi
Remont podłogi na gruncie to operacja na otwartym sercu budynku. Odkrywamy konstrukcję, która przez dekady zmagała się z siłami natury. Jednak nawet najlepiej wykonana "ciepła" podłoga może stracić swój potencjał, jeśli zaniedbamy jej styki z innymi elementami konstrukcji – przede wszystkim ze ścianami fundamentowymi. Połączenie izolacji podłogi ze ścianami to krytyczny detal, który decyduje o tym, czy uda nam się całkowicie wyeliminować mostki termiczne i wilgotnościowe, czy też stworzymy permanentne drogi ucieczki ciepła i wnikania wilgoci.
Wyobraźcie sobie ciepły koc, którym przykrywacie się zimą. Jeśli macie szczeliny na brzegach, przez które podwiewa chłodne powietrze, mimo grubości koca, nadal czujecie dyskomfort. Tak samo działa to w budynku. Izolacja podłogi i izolacja ścian działają jak ten koc, ale jeśli ich styki nie są szczelne i ciągłe, tworzą się zimne miejsca – mostki termiczne. W tych miejscach ciepło ucieka najszybciej, a różnica temperatur może prowadzić do kondensacji pary wodnej zawartej w powietrzu wewnętrznym, a to z kolei prosta droga do zawilgocenia materiałów i rozwoju pleśni.
Hydroizolacja pozioma podłogi (ta papa lub folia leżąca na chudziaku) musi zostać połączona ze zrobioną wcześniej (lub jednocześnie) hydroizolacją pionową ścian fundamentowych. Najlepszym sposobem jest wywinięcie materiału hydroizolacyjnego z poziomu podłogi w górę, na powierzchnię ściany fundamentowej, na wysokość kilkudziesięciu centymetrów (minimum 15 cm, ale 30 cm daje większy margines bezpieczeństwa). Tworzy to "wanienkę" czy "misę", w której leży cała konstrukcja podłogi. Papa termozgrzewalna jest zgrzewana do uprzednio zagruntowanej ściany, tworząc solidne i trwałe połączenie. Folia PE jest wywijana i doklejana do ściany np. taśmą butylową lub specjalnym klejem, a następnie zazwyczaj zabezpieczana listwą dociskową lub tynkiem.
Równie ważne jest połączenie izolacji termicznej podłogi z izolacją termiczną ściany fundamentowej. Na zewnętrznej stronie ściany fundamentowej, poniżej poziomu gruntu i kilkadziesiąt centymetrów powyżej, powinna znajdować się warstwa izolacji termicznej, zazwyczaj w postaci płyt polistyrenu ekstrudowanego (XPS), który charakteryzuje się niską nasiąkliwością i wytrzymałością na ściskanie. Izolacja podłogi na gruncie powinna stykać się lub zachodzić na tę izolację pionową ściany, tworząc ciągłość. Styki płyt izolacyjnych powinny być minimalizowane i starannie spasowane, a wszelkie szczeliny między izolacją podłogi a izolacją ściany fundamentowej wypełnione np. pianką montażową o niskiej rozprężności lub szczeliwem.
W starych domach ściany fundamentowe bywają różne – murowane z kamienia, cegły, czasem nawet drewniane pale. Ich powierzchnia często jest nierówna. To dodatkowo utrudnia wykonanie szczelnej i ciągłej izolacji. Czasem konieczne jest wyrównanie powierzchni ściany tynkiem cementowym lub masą bitumiczną przed ułożeniem hydroizolacji pionowej i doklejeniem izolacji termicznej (XPS). Starannie przemyślany i wykonany detal styku podłoga-ściana to gwarancja, że warstwa termoizolacyjna i hydroizolacyjna podłogi będą w pełni skuteczne, a my unikniemy przykrych niespodzianek w postaci zimnych i wilgotnych narożników przy podłodze.
Brak ciągłości izolacji w tym miejscu jest jednym z głównych powodów, dla których podłogi na gruncie w starych, remontowanych domach pozostają zimne pomimo położenia grubej warstwy izolacji. Ciepło "omija" izolację podłogową, uciekając przez niezaizolowane styki ze ścianami fundamentowymi i dalej w grunt lub na zewnątrz przez ściany fundamentowe. To zjawisko "mostka termicznego" jest tym bardziej dotkliwe, im większa jest różnica temperatur między wnętrzem domu a gruntem i powietrzem zewnętrznym.
Co więcej, niedokładne połączenie izolacji ze ścianami w aspekcie hydroizolacji pozwala wilgoci z gruntu podciągać się w górę po ścianach, prowadząc do ich zawilgocenia. Izolacja pozioma na wysokości ławy fundamentowej (przecinająca ścianę fundamentową) powinna również szczelnie łączyć się z izolacją podłogi i pionową izolacją fundamentu, tworząc kompleksową barierę przed wilgocią. Jest to zasada "szczelnej wanny" – cały budynek, a przynajmniej jego najniższa część, powinien być zanurzony w tej szczelnej powłoce izolacyjnej.
Dobry projekt remontu podłogi powinien szczegółowo uwzględniać detale tych połączeń. W praktyce często stosuje się dodatkowe warstwy uszczelniające w "kącie" między podłogą a ścianą, np. masy uszczelniające na bazie polimerów lub bitumów, które zapewniają elastyczność i szczelność nawet przy niewielkich ruchach konstrukcji. Płyty izolacyjne podłogi powinny być dociśnięte do izolacji ściany, a przerwa między nimi wypełniona, aby zapobiec konwekcyjnemu przepływowi powietrza (i ciepła).
Remontując podłogę na gruncie w starym domu, pomyślcie o fundamentach i ścianach nie jako o odrębnych elementach, ale jako o częściach jednego systemu, który ma zapewnić szczelność i ciepło całej dolnej partii budynku. Tylko holistyczne podejście, gdzie izolacja podłogi i izolacja ścian fundamentowych są projektowane i wykonywane jako spójny system, pozwala na pełne wykorzystanie potencjału termoizolacji i długoterminową ochronę przed wilgocią. Ten pozornie mały detal decyduje o wielkim komforcie życia i zdrowiu konstrukcji domu na długie lata.