Kompleksowy remont starej podłogi z desek - Poradnik 2025
Odkurzcie marzenia o przywróceniu życia dawnym wnętrzom. Remont starej podłogi z desek to podróż w czasie, często pełna niespodzianek, gdzie odkrywamy ukryte piękno historycznego drewna. To proces wymagający cierpliwości i precyzji, ale nagroda w postaci odnowionej, szlachetnej powierzchni, rekompensuje każdy wysiłek. Kluczowa odpowiedź tkwi w starannym przygotowaniu i odpowiednim wykończeniu desek.
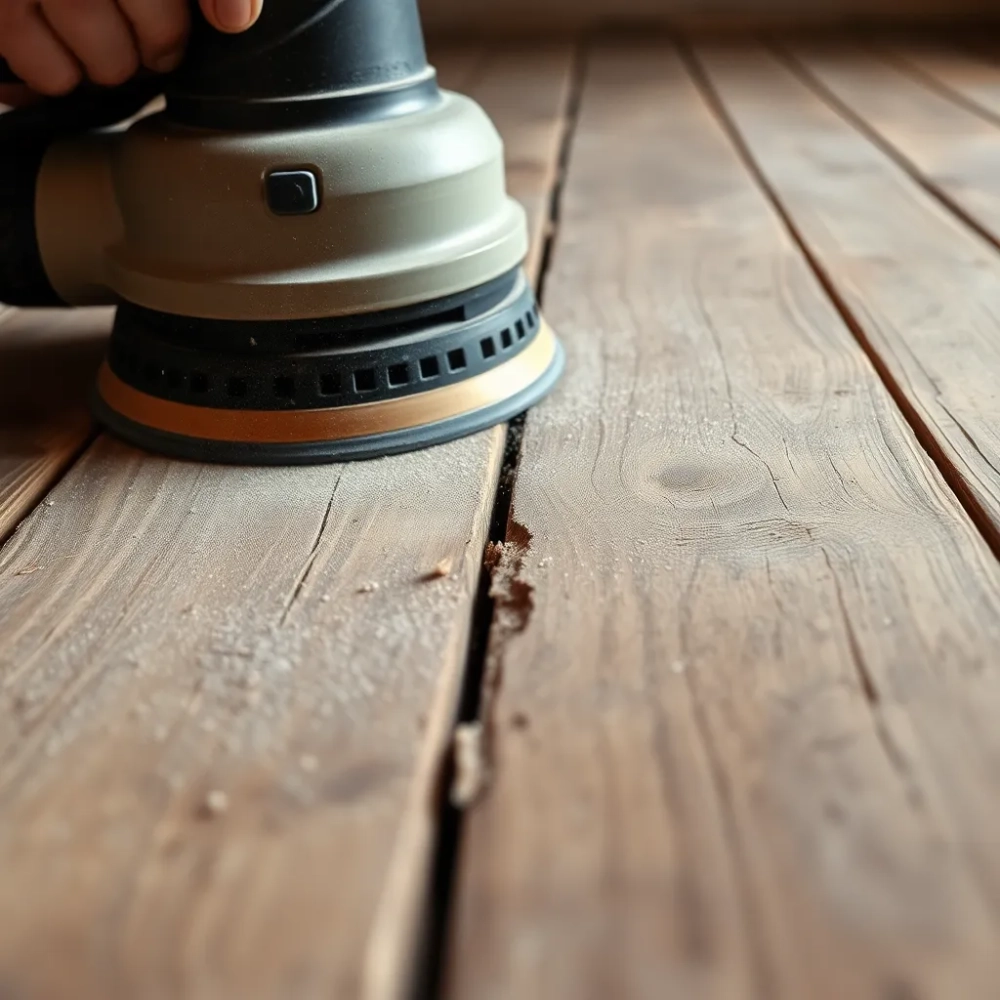
Analizując dane zgromadzone z wielu projektów renowacyjnych drewnianych podłóg na przestrzeni lat, możemy dostrzec pewne powtarzające się wzorce dotyczące materiałów i wyzwań.
Typ Podłogi (średnia wieku) | Dominujący Problem | Średnie Zużycie Wypełniacza (kg/m²) | Średnie Zużycie Papieru Ściernego (arkusze/m² - grube ziarno) |
---|---|---|---|
Deska sosnowa (>50 lat) | Luźne deski, duże szczeliny | 0.2 - 0.4 | 0.5 - 0.8 |
Parkiet dębowy (>60 lat) | Zużycie wierzchniej warstwy, pojedyncze ubytki | 0.1 - 0.2 | 0.4 - 0.6 |
Deska dębowa (>70 lat) | Głębokie rysy, przebarwienia | 0.15 - 0.3 | 0.6 - 1.0 |
Podłoga mieszana (>80 lat) | Wiele problemów, różny stopień zniszczenia | 0.3 - 0.5+ | 0.7 - 1.2+ |
Te dane wyraźnie pokazują, że starsze i bardziej miękkie gatunki drewna, jak sosna, często generują większe zużycie materiałów, zwłaszcza wypełniaczy potrzebnych do zniwelowania szerokich szczelin i większych ubytków, które nagromadziły się przez dekady eksploatacji.
Zrozumienie tych tendencji jest kluczowe przy planowaniu remontu, pozwala realistycznie ocenić zakres prac i potrzebne materiały jeszcze przed rozpoczęciem projektu.
Przedstawione dane statystyczne z licznych renowacji dają pewne ramy do przewidywania zużycia materiałów, jednak stan faktyczny każdej indywidualnej podłogi może znacząco odbiegać od średniej, wymagając elastyczności w planowaniu i budżetowaniu.
Intensywność prac przygotowawczych i szlifierskich zależy w ogromnej mierze od ilości starych warstw wykończenia (lakier, wosk, farba), głębokości zniszczeń, a także od tego, czy deski są stabilnie zamocowane do legarów lub podłoża.
Warto podkreślić, że te liczby stanowią jedynie punkt wyjścia do dokładniejszej wyceny i zaplanowania logistyki remontu, podkreślając potrzebę szczegółowej inspekcji przed przystąpieniem do działania.
Niektóre podłogi mogą wymagać znacznie większej ilości szpachlowania lub intensywniejszego szlifowania, jeśli przez lata były niewłaściwie konserwowane lub poniosły poważne uszkodzenia strukturalne.
Przygotowanie starej podłogi do remontu
Proces przygotowania starej drewnianej podłogi do remontu to fundament, od którego zależy ostateczny sukces i trwałość renowacji.
To etap, którego absolutnie nie wolno lekceważyć ani przyspieszać – jak mawia stare porzekadło budowlane, "pośpiech jest złym doradcą", a w przypadku podłóg desek to prawda do bólu.
Wszelkie niedociągnięcia na tym etapie, czy to w stabilizacji desek, czy w usunięciu zanieczyszczeń, prędzej czy później ujawnią się, psując efekt nawet najlepiej wykonanego szlifowania i wykończenia.
Zaczynamy od opróżnienia pomieszczenia do absolutnego zera – nie może zostać żaden mebel, obraz, czy nawet listwa przypodłogowa, jeśli ma zostać wymieniona lub poddana renowacji razem z podłogą.
Następnie przechodzimy do szczegółowej inspekcji każdego centymetra kwadratowego powierzchni.
Szukamy luźnych desek, skrzypiących elementów, wystających gwoździ, wkrętów, głębokich pęknięć, ubytków, a także miejsc, gdzie podłoga ugina się pod ciężarem.
Luźne deski muszą zostać ponownie solidnie przytwierdzone, najlepiej za pomocą wkrętów do drewna, które należy wpuścić poniżej lica deski.
Skrzypienie często wynika z tarcia luźnych desek o legary lub sąsiadujące deski; ich ponowne mocowanie zazwyczaj rozwiązuje problem, choć czasem konieczne jest dodanie klinów lub zastosowanie specjalistycznych klejów.
Wystające elementy metalowe, takie jak gwoździe czy stare zszywki od wykładziny, to bezwzględni wrogowie maszyn szlifierskich – muszą zostać bezlitośnie usunięte lub wbite głęboko w drewno (min. 3-4 mm poniżej powierzchni), tak aby nie uszkodzić papieru ściernego ani samego bębna cykliniarki.
Zabijaki do gwoździ o różnej średnicy są tutaj niezastąpione narzędziem.
Przypadek z życia: Znajomy, remontując starą podłogę, przeoczył jeden jedyny mały gwóźdź schowany w szparze – kosztowało go to poważne uszkodzenie drogiego papieru i wymianę elementu cykliniarki.
Każdy metalowy element musi zostać namierzony i zneutralizowany, czasem nawet detektorem metalu.
Kolejnym krokiem jest gruntowne czyszczenie powierzchni z kurzu, brudu, resztek kleju, taśm, wosku czy innych zanieczyszczeń.
Jeśli na podłodze znajdowała się wykładzina dywanowa, często pozostają po niej uporczywe resztki kleju, które mogą wymagać zdrapania ręcznego lub użycia specjalnych rozpuszczalników do klejów.
Woskowane podłogi mogą potrzebować przetarcia specjalnym preparatem do usuwania wosku, co ułatwi późniejsze szlifowanie.
Brud i tłuszcz mogą głęboko wniknąć w strukturę drewna, zwłaszcza w miejscach często użytkowanych, jak przejścia czy okolice kuchni – usunięcie ich przed szlifowaniem zapobiega wnikaniu ich w pory drewna podczas cyklinowania i powstawaniu trudnych do usunięcia plam.
Szczególnej uwagi wymagają głębokie ubytki, dziury po usuniętych elementach instalacji, czy pęknięcia szersze niż 2-3 mm.
Mniejsze szczeliny między deskami zostaną zazwyczaj wypełnione masą szpachlową powstałą ze zmieszania pyłu drzewnego zebranego podczas pierwszego etapu szlifowania z dedykowanym spoiwem.
Większe ubytki często wymagają wklejenia fragmentów drewna o identycznym gatunku i słojach, dopasowanych jak elementy układanki – to technika wymagająca precyzji i cierpliwości, ale dająca najbardziej estetyczny i trwały rezultat.
Ważne jest, aby drewno używane do łatania miało zbliżoną wilgotność do desek podłogowych, aby uniknąć późniejszych naprężeń i pęknięć.
Niekiedy napotykamy na poważnie uszkodzone deski, spróchniałe, zniszczone przez insekty lub z głębokimi pęknięciami biegnącymi przez całą grubość – takie deski kwalifikują się do wymiany.
Wymiana deski polega na ostrożnym wycięciu uszkodzonego fragmentu, unikając naruszenia sąsiadujących desek i legarów, a następnie wklejeniu lub przybiciu nowego elementu.
Szukanie starych desek z rozbiórek, które będą pasować do historycznej podłogi wiekiem i wyglądem, to często najlepsze rozwiązanie, choć wymaga detektywistycznych zdolności.
Użycie nowego drewna o identycznym gatunku jest możliwe, ale może być widoczna różnica w kolorze i strukturze słojów przez wiele lat, dopóki nowe drewno nie "postarzeje się" w naturalny sposób.
Kontrola wilgotności drewna podłogowego jest fundamentalnym krokiem przed rozpoczęciem szlifowania i wykończenia.
Idealna wilgotność drewna przed cyklinowaniem i lakierowaniem powinna wynosić od 8% do 12%.
Wyższa wilgotność może spowodować "wałkowanie" się papieru ściernego i utrudnić szlifowanie, a co gorsza, po wyschnięciu drewna mogą pojawić się nowe szczeliny lub wypaczenia już po nałożeniu warstw wykończeniowych.
Miernik wilgotności drewna to inwestycja, która szybko się zwraca, zapobiegając kosztownym błędom.
Zabezpieczenie drzwi i innych elementów pomieszczenia, które mają zostać w nim na czas remontu (np. stała zabudowa), jest koniecznością – folia malarska i taśma powinny szczelnie osłonić wszystko, co nie ma zostać pokryte pyłem.
Otwory wentylacyjne i szpary pod drzwiami prowadzącymi do innych pomieszczeń również powinny być uszczelnione, aby ograniczyć rozprzestrzenianie się pyłu po całym domu – mimo stosowania cykliniarek z systemami odpylającymi, pewna jego ilość zawsze się przedostaje.
Pamiętajmy, że pył drzewny jest łatwopalny, a pył z niektórych gatunków drewna może być toksyczny lub uczulający – odpowiednie środki ochrony dróg oddechowych są absolutnie kluczowe.
Podsumowując etap przygotowawczy, jego zakres jest często niedoszacowywany przez osoby bez doświadczenia – bywa, że zajmuje on tyle samo czasu co szlifowanie i wykończenie razem wzięte, zwłaszcza przy bardzo zaniedbanych podłogach.
Solidne, przemyślane i skrupulatne przygotowanie podłogi to obietnica, że kolejne etapy remontu przebiegną gładko, a efekt końcowy będzie cieszył oko przez lata, pokazując pełnię naturalnego piękna drewna ukrytego pod warstwami historii.
Sprawdzenie instalacji elektrycznych i hydraulicznych przebiegających pod podłogą, o ile mamy do nich dostęp lub podejrzewamy ich istnienie pod deskami, może zapobiec katastrofie podczas prac remontowych.
Narzędzia ręczne, takie jak dłuta, młotek, łom do desek, packi do szpachlowania i szlifierki kątowe z odpowiednimi nasadkami do czyszczenia trudno dostępnych miejsc, są tak samo ważne, jak duża cykliniarka bębnowa na kolejnych etapach.
Szlifowanie (cyklinowanie) starej podłogi z desek
Szlifowanie, powszechnie zwane cyklinowaniem, to serce kompleksowej renowacji drewnianej podłogi – to właśnie na tym etapie usuwane są stare, zużyte warstwy wykończenia, głębokie zarysowania, wgniecenia, plamy i wyrównywana jest cała powierzchnia desek.
Proces ten odkrywa surowe drewno, gotowe na nowe życie i zabezpieczenie, wydobywając jego naturalną barwę i rysunek słojów.
To zadanie wymagające precyzji, cierpliwości i przede wszystkim właściwego użycia profesjonalnego sprzętu – błąd na tym etapie może pozostawić trwałe, widoczne ślady.
Główne narzędzie to cykliniarka bębnowa lub taśmowa, maszyna o dużej mocy i masie (często przekraczającej 60-80 kg), przeznaczona do pracy na dużych powierzchniach.
Pracę rozpoczyna się od papieru ściernego o niskiej gradacji (grubym ziarnie), najczęściej 40 lub 60.
Wybór początkowej gradacji zależy od stanu podłogi – bardzo zniszczone, nierówne podłogi z wieloma warstwami lakieru mogą wymagać papieru o gradacji 24 lub 36, ale użycie zbyt niskiej gradacji na początku na stosunkowo równej podłodze może spowodować niepotrzebne uszkodzenie desek w postaci głębokich rys.
Papier o grubej gradacji szybko usuwa starą warstwę wykończenia i wyrównuje poziom desek, niwelując niewielkie wybrzuszenia czy wgniecenia.
W przypadku podłóg z desek, cyklinowanie wykonuje się zazwyczaj wzdłuż słojów drewna, czyli równolegle do dłuższej krawędzi desek.
Praca cykliniarką wymaga płynnych, zachodzących na siebie pasów, prowadzonych ze stałą prędkością – zatrzymanie maszyny w miejscu z opuszczonym bębnem prowadzi do powstania charakterystycznego "dołka", czyli przeszlifowania.
Rozpoczęcie i zakończenie każdego pasa szlifowania powinno odbywać się z uniesionym bębnem, delikatnie opuszczanym na podłogę już w ruchu i podnoszonym przed zatrzymaniem maszyny lub przed zmianą kierunku.
Typowa sekwencja szlifowania obejmuje kilka przejść maszyny głównej z sukcesywnie wyższą gradacją papieru – np. 40, 60, 80, a końcowe szlifowanie to gradacja 100 lub 120.
Stopniowanie papieru ściernego jest krytycznie ważne; przeskoczenie gradacji (np. z 40 od razu na 100) nie usunie rys pozostawionych przez grubsze ziarno i sprawi, że będą one widoczne po wykończeniu.
Po zakończeniu szlifowania maszyną główną na całej powierzchni przystępuje się do szlifowania krawędzi i narożników.
Do krawędzi używa się specjalnej cykliniarki krawędziowej, mniejszej maszyny umożliwiającej dotarcie blisko ścian.
Sekwencja gradacji papieru na krawędziarce powinna odpowiadać gradacji użytej na maszynie głównej – zaczynamy od 40/60, kończąc na 100/120.
Narożniki i miejsca trudno dostępne, gdzie maszyny nie dotrą (np. wokół rur, pod grzejnikami), szlifuje się ręcznie lub przy użyciu małej szlifierki oscylacyjnej lub delta.
Między kolejnymi przejściami cykliniarką, a zwłaszcza przed rozpoczęciem szlifowania papierem o drobnej gradacji, kluczowe jest dokładne odkurzenie podłogi.
Pozostawione na powierzchni ziarenka gruboziarnistego pyłu działają jak dodatkowe, niekontrolowane "papierki" ścierne podczas pracy z drobniejszym ziarnem, psując efekt gładkiej powierzchni.
Wysokiej jakości odkurzacz budowlany z dobrym systemem filtracji (najlepiej z filtrem HEPA, zwłaszcza na końcowych etapach) jest niezbędny.
Wspomniany wcześniej pył drzewny zebrany podczas pierwszego przejścia papierem 40 lub 60 jest następnie mieszany ze specjalnym spoiwem, tworząc masę szpachlową.
Ta masa jest używana do wypełniania mniejszych szczelin między deskami oraz drobnych ubytków.
Szpachlowanie wykonuje się po pierwszym lub drugim szlifowaniu (grubym), tak aby masa mogła wniknąć w pory drewna i szczeliny.
Po wyschnięciu masy szpachlowej (czas schnięcia zależy od produktu i grubości warstwy, zazwyczaj kilka godzin) przystępuje się do kolejnych etapów szlifowania drobniejszym papierem, które usuną nadmiar szpachli i ostatecznie wygładzą powierzchnię.
Powierzchnia po ostatnim szlifowaniu powinna być idealnie gładka w dotyku, bez wyczuwalnych rys, "fali" od maszyny czy śladów przeszlifowania.
Ostateczny efekt szlifowania zależy w dużej mierze od doświadczenia operatora maszyny – niewłaściwa technika może pozostawić trwałe wady.
Kontrola jakości szlifowania powinna odbywać się przy dobrym, najlepiej bocznym oświetleniu, które uwidacznia wszelkie nierówności i niedociągnięcia.
Cyklinowanie generuje ogromne ilości drobnego pyłu, który, choć w większości pochłaniany przez systemy odpylające maszyn, unosi się w powietrzu i osiada wszędzie.
Maseczki przeciwpyłowe (co najmniej FFP2, najlepiej FFP3), okulary ochronne i słuchawki (maszyny są bardzo głośne) to absolutnie podstawowe wyposażenie ochronne, którego nie wolno zaniedbać.
Dobre wietrzenie pomieszczenia podczas i po pracy, o ile jest możliwe i nie wpłynie negatywnie na wilgotność drewna, pomaga w usuwaniu pyłu.
Profesjonalne szlifowanie podłogi wymaga nie tylko maszyn, ale przede wszystkim umiejętności i wiedzy o zachowaniu drewna podczas obróbki.
Czystość na tym etapie jest synonimem jakości – każde ziarenko piasku czy pyłu pozostawione na powierzchni lub pod papierem może spowodować rysy, które trzeba będzie usuwać przez powtórzenie szlifowania, cofając się do grubszych gradacji.
Wykończenie podłogi po szlifowaniu – lakier, olej czy wosk?
Po etapie szlifowania podłoga zyskuje surowe, czyste lico drewna, jednak bez odpowiedniego zabezpieczenia jest bardzo podatna na uszkodzenia, zabrudzenia i wilgoć.
Wykończenie podłogi to kluczowy etap, który nie tylko chroni drewno, ale także decyduje o finalnym wyglądzie i charakterze powierzchni.
Najpopularniejsze metody wykończenia to lakierowanie, olejowanie i woskowanie, każda z nich ma swoje specyficzne właściwości, zalety i wady, a wybór między nimi powinien być podyktowany przeznaczeniem pomieszczenia, oczekiwanym efektem wizualnym oraz gotowością na przyszłą pielęgnację.
Wybór sposobu wykończenia podłogi jest decyzją długoterminową, mającą wpływ na trwałość i sposób użytkowania podłogi przez kolejne lata.
Lakierowanie tworzy na powierzchni drewna trwałą, twardą powłokę.
Lakiery do podłóg są dostępne w różnych wariantach: na bazie rozpuszczalników (bardzo trwałe, ale o silnym zapachu i dłuższym czasie schnięcia/utwardzania) oraz coraz popularniejsze lakiery wodorozcieńczalne (mniej zapachu, szybsze schnięcie, bardziej ekologiczne, ale czasem nieco mniej odporne na ścieranie w porównaniu do najlepszych lakierów rozpuszczalnikowych).
Lakier tworzy film na powierzchni, który skutecznie chroni drewno przed wnikaniem brudu, wody i substancji plamiących.
Lakiery występują w różnych stopniach połysku – od matowych, przez półmat, satynę, po wysoki połysk – co pozwala uzyskać pożądany efekt wizualny.
Aplikacja lakieru zazwyczaj wymaga nałożenia 2-3 warstw, przy czym po pierwszej lub drugiej warstwie zaleca się tzw. międzywarstwowe szlifowanie (papierem o bardzo drobnej gradacji, np. 180-220) w celu usunięcia uniesionych włókien drewna i zapewnienia lepszej przyczepności kolejnej warstwy.
Pomiędzy nakładaniem kolejnych warstw konieczne jest przestrzeganie zalecanego przez producenta czasu schnięcia (np. 2-4 godziny dla lakierów wodnych).
Pełne utwardzenie lakieru, podczas którego podłoga uzyskuje ostateczną odporność na obciążenia i zarysowania, trwa znacznie dłużej – od kilku dni do nawet dwóch tygodni, w zależności od typu lakieru i warunków otoczenia (temperatura, wilgotność).
W tym czasie należy unikać stawiania ciężkich mebli i intensywnego użytkowania podłogi.
Olejowanie nie tworzy na powierzchni warstwy, lecz wnika głęboko w strukturę drewna, wzmacniając je od środka i nadając mu naturalny wygląd.
Podłoga olejowana jest przyjemna w dotyku, zachowuje naturalną fakturę drewna i "oddycha", co pozytywnie wpływa na mikroklimat pomieszczenia.
Oleje podkreślają naturalną barwę drewna, często ją pogłębiając i czyniąc słoje bardziej wyrazistymi.
Oleje są łatwiejsze w lokalnych naprawach niż lakier – pojedyncze rysy czy zabrudzenia można często przeszlifować i ponownie zaolejować, podczas gdy uszkodzony lakier zazwyczaj wymaga przeszlifowania i ponownego lakierowania całego elementu lub nawet pomieszczenia.
Z drugiej strony, podłoga olejowana wymaga częstszej pielęgnacji i konserwacji niż podłoga lakierowana.
Powinna być regularnie (np. co kilka lat, w zależności od intensywności użytkowania) ponownie olejowana, aby utrzymać swoje właściwości ochronne i estetyczne.
Jest też bardziej podatna na plamy z substancji takich jak wino, kawa czy tłuszcze, które mogą wniknąć w drewno, jeśli nie zostaną szybko usunięte.
Aplikacja oleju jest zazwyczaj prostsza niż lakieru – po naniesieniu produktu (wałkiem, pędzlem lub pacą) nadmiar, który nie wchłonął się w drewno, jest usuwany po określonym czasie (zgodnie z instrukcją producenta) za pomocą czystych padów lub ściereczek, a następnie często nanosi się drugą, cienką warstwę.
Woskowanie, często w połączeniu z olejowaniem (tzw. olejowosk), zapewnia miękkie, naturalne wykończenie i aksamitną w dotyku powierzchnię.
Wosk podobnie jak olej wnika w pory drewna, ale dodatkowo tworzy na powierzchni cienką, ochronną warstwę, która nadaje delikatny połysk lub satynowe wykończenie.
Podłogi woskowane i olejowoskowane charakteryzują się pięknym, naturalnym wyglądem i są cenione w pomieszczeniach o rustykalnym lub tradycyjnym charakterze.
Są jednak mniej odporne na ścieranie i wilgoć niż podłogi lakierowane, wymagają regularnej konserwacji specjalnymi środkami na bazie wosku.
Wybór między lakierem, olejem a woskiem zależy także od gatunku drewna.
Niektóre gatunki, jak np. jesion czy dąb, świetnie przyjmują zarówno lakier, jak i olej, podczas gdy inne, np. drewno egzotyczne bogate w olejki, mogą wymagać specjalnych przygotowań lub dedykowanych produktów.
Styl życia i przeznaczenie pomieszczenia są decydujące – lakier będzie lepszym wyborem do miejsc intensywnie użytkowanych (korytarze, salony w dużych rodzinach), gdzie liczy się maksymalna trwałość i łatwość w codziennym sprzątaniu.
Olej sprawdzi się w pomieszczeniach o spokojniejszym ruchu (sypialnie, gabinety) lub tam, gdzie ceni się naturalność drewna i możliwość łatwych, punktowych napraw.
Rodzaj wykończenia podłogi ma fundamentalne znaczenie dla jej późniejszej konserwacji.
Pamiętajmy, że każdy typ wykończenia wymaga używania dedykowanych środków czyszczących i pielęgnacyjnych, które nie zniszczą powłoki i pozwolą jej służyć jak najdłużej.
Koszty remontu starej podłogi i kiedy warto wynająć fachowców
Koszty remontu starej drewnianej podłogi to temat rzeka, który potrafi zaskoczyć niejednego, zwłaszcza gdy stan desek okazuje się gorszy, niż pierwotnie zakładano.
Ogólna zasada mówi, że koszty można podzielić na materiałowe, koszt wynajmu sprzętu (jeśli robimy sami) lub robocizny (jeśli wynajmujemy fachowców).
Przyjmuje się, że kompletny remont podłogi wykonany przez profesjonalną ekipę to zazwyczaj koszt w przedziale od 80 do 150+ złotych za metr kwadratowy, ale jest to wartość bardzo płynna.
Ten przedział często nie obejmuje kosztu materiałów wykończeniowych (lakieru, oleju), które wybiera i kupuje inwestor, choć niektórzy fachowcy oferują kompleksowe usługi z własnymi materiałami.
Koszty materiałów na metr kwadratowy mogą wynosić od 30 do nawet 80 złotych i więcej, w zależności od jakości i rodzaju wybranych produktów.
Papier ścierny to koszt kilku do kilkunastu złotych za arkusz/rolkę, a na jeden metr kwadratowy podłogi zużywa się go w ilości kilku do kilkunastu sztuk/fragmentów, przechodząc przez całą sekwencję gradacji.
Koszty wypełniaczy do drewna są stosunkowo niewielkie w przeliczeniu na m², chyba że szczeliny są bardzo duże i liczne.
Największą pozycję w kosztach materiałów stanowią zazwyczaj lakiery, oleje lub olejowoski – dobrej jakości produkty mogą kosztować od kilkudziesięciu do ponad stu złotych za litr, a wydajność jednego litra to zazwyczaj od 8 do 15 m² na jedną warstwę.
Jeśli zdecydujemy się na samodzielny remont, dochodzi koszt wynajmu specjalistycznych maszyn – cykliniarki bębnowej/taśmowej i krawędziowej.
Wynajem dużej cykliniarki to koszt rzędu 100-200 złotych za dobę, krawędziarki ok. 80-150 złotych za dobę.
Do tego dochodzą koszty zakupu papieru ściernego w systemie wynajmującego (zazwyczaj lekko zawyżone, ale mamy pewność, że pasuje do maszyny) oraz niezbędnych akcesoriów, takich jak maseczki, okulary, folie ochronne, wałki do lakieru czy pędzle do oleju.
Samodzielne działanie może wydawać się znacznie tańsze na papierze, eliminując koszt robocizny, ale wymaga poświęcenia znacznej ilości czasu i wysiłku fizycznego, a także wiąże się z ryzykiem popełnienia błędów, które mogą zwiększyć ostateczne koszty.
Kiedy zatem warto rozważyć wynajęcie fachowców? Odpowiedź często sprowadza się do kombinacji kilku czynników.
Po pierwsze, skomplikowany stan podłogi – jeśli deski są bardzo nierówne, mocno uszkodzone, jest ich wiele do wymiany, lub jeśli mamy do czynienia z podłogą o nietypowym wzorze (np. jodła, szachownica) czy ze starym parkietem wymagającym precyzyjnej naprawy i cyklinowania.
Po drugie, brak czasu i doświadczenia – cyklinowanie to nie jest zadanie na jeden weekend, wymaga pewnych umiejętności, wyczucia maszyny i wiedzy o procesie, a nieumiejętne posługiwanie się sprzętem może nieodwracalnie zniszczyć podłogę.
Po trzecie, duże powierzchnie – remont kilkudziesięciu metrów kwadratowych podłogi samodzielnie jest przedsięwzięciem wyczerpującym i czasochłonnym.
Profesjonalne firmy dysponują nie tylko odpowiednim sprzętem (często wyższej klasy, z lepszym odpylaniem), ale przede wszystkim mają doświadczenie, które pozwala im szybko i skutecznie ocenić stan podłogi, dobrać odpowiednią technologię szlifowania i wykończenia oraz uniknąć typowych błędów.
Studium przypadku: Rodzina K., próbując zaoszczędzić, wynajęła cykliniarkę do renowacji 30m² salonu.
Po dwóch dniach zmagań, z przeszlifowaną podłogą, dołkami i "falą" od maszyny, wezwali fachowca, który musiał ponownie szlifować całą powierzchnię grubym papierem, aby naprawić błędy, co ostatecznie podwoiło pierwotnie zakładane koszty.
Wartość dodana profesjonalnych usług często polega na gwarancji jakości i spokoju ducha.
Nie można też zapomnieć o czynnikach zewnętrznych wpływających na koszty – lokalizacja (ceny usług różnią się między regionami), dostępność ekip (w "gorących" sezonach ceny mogą być wyższe), a także konieczność przeprowadzenia dodatkowych prac, np. wymiany legarów czy izolacji podłogi, które znacząco zwiększą kosztorys renowacji desek.
Zanim podejmiecie decyzję, czy zrobić remont samodzielnie, czy zlecić go fachowcom, warto zrobić dokładną kalkulację.
Porównajcie szacunkowe koszty materiałów i wynajmu sprzętu z cenami za metr kwadratowy podawanymi przez profesjonalne firmy, biorąc pod uwagę również wartość swojego czasu i poziom doświadczenia.
Poproszenie o kilka niezależnych wycen od różnych firm pozwala zorientować się w rynkowych realiach i wybrać najkorzystniejszą opcję.